AI vs Traditional Automation: Which One You Should Choose For Your Manufacturing Business?
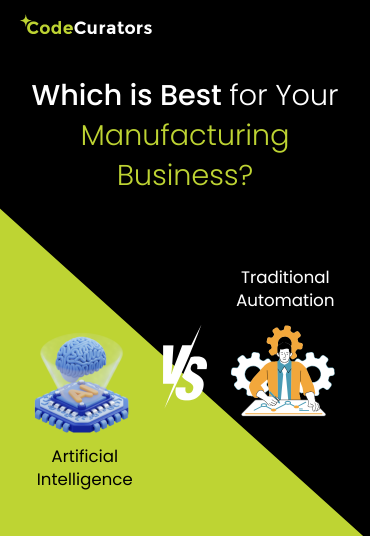
AI vs Traditional Automation: Which One You Should Choose For Your Manufacturing Business?
The modern manufacturing sector exists under continuous pressure to enhance its operational efficiency and lower their costs while maintaining global market competitiveness. The sector has experienced automation for decades, yet Artificial Intelligence (AI) lately brings transformative changes beyond traditional automated systems. At CodeCurators, we help manufacturers harness these AI-driven innovations to stay ahead of the curve and unlock new levels of productivity.
Different manufacturing businesses should choose between implementing artificial intelligence and traditional automation systems to achieve maximum productivity and endure long-term success. This article compares both techniques starting from their basic characteristics through their uses and benefits, and ends with guidance on selecting the most fitting option for your manufacturing enterprise.
Understanding Traditional Automation
Machines coupled with programmed control systems make up traditional automation which requires minimal human labor for repetitive work. The manufacturing process includes assembly lines which utilize robotic welding arms together with conveyor belts and CNC machines that fulfill predefined cutting operations. Such systems operate with efficiency but have limitations when applied to conditions different from their initial programming.
In manufacturing, traditional automation is commonly used for:
- Welding and assembly of components
- Installing prefabricated parts or modules
- Painting and finishing processes
- Quality checks using vision sensors
These systems are built to operate with high precision and speed. However, they often lack the flexibility to adapt to changes in product design, customer customization, or supply chain disruptions.
What is AI in Manufacturing?
The technology known as AI, or artificial intelligence, creates machine systems that duplicate human reasoning capabilities. Artificial intelligence operates differently from standard automated systems since it processes data to make decisions and learns from feedback, leading to constant performance enhancement. The application of AI technology in manufacturing allows companies to perform smart operations such as predictive maintenance and intelligent process control together with dynamic scheduling.
Manufacturers integrate artificial intelligence algorithms into their essential business processes, including production and logistics and customer service, and quality assurance.
AI systems can:
- Predict when machinery is likely to fail and schedule maintenance proactively
- Optimize production schedules based on real-time inventory and order data
- Use computer vision to detect defects invisible to the human eye
- Personalize configurations based on customer preferences
- Reduce energy consumption by adjusting systems dynamically
Comparing Traditional Automation and AI
1. Flexibility
The main strength of traditional automation systems lies in efficiently completing repeated operations in stable production environments. Manufacturing businesses that produce large amounts of homogeneous products can find traditional automation systems to be a suitable solution.
However, AI offers unparalleled flexibility. AI-powered systems modify their operational patterns through real-time process information.
When customers demand custom versions of your products, artificial intelligence enables your machines to adjust operations while bypassing workflow reprogramming steps. The dynamic advantage of AI becomes useful for organizations that need frequent design modifications alongside product customization requirements.
2. Scalability
Traditional automation solutions demand a major capital outlay to handle operational expansion since they need structural modifications. Business expansion through scaling requires organizations to add new equipment, workspace, and human personnel.
The capability of artificial intelligence enables scalability because users can scale their operations by upgrading software, along with more efficient use of existing resources. An AI scheduling system operates automatically to maximize productivity by cutting down unproductive delays and system obstructions while needing no hardware investments or additions.
3. Cost
The cost structure of traditional automation systems remains obvious to all users. Machines and programming, along with installation as well as maintenance, represent the typical cost of the investment. The running costs after implementation become specific with lower expenses than human resources, and maintenance requirements are foreseeable.
Including sensors, machine learning models, and data infrastructure creates high implementation expenses that organizations must pay to start using AI systems. Fundamental cost reductions appear substantially in the long term. When AI systems come into action, they shorten manufacturing stops, reduce production flaws, and maximize operational efficiency, which results in reduced expenses for each product made.
The initial cost advantage of robotic automation proves deceptive because AI generates higher return on investment benefits throughout the long term.
4. Data Utilization
Traditional automation systems generate some data, like machine run time or error logs, but they don’t analyze it. That data is often underutilized.
AI thrives on data. It collects, processes, and learns from massive data sets. In manufacturing, AI can detect trends in customer orders, predict which product variants are gaining popularity, or identify patterns in defects that help improve design.
Data is the new oil, and AI is the engine that puts it to work.
Applications of AI in Manufacturing
1. Predictive Maintenance
Manufacturing involves heavy machinery, welding robots, conveyor systems, and finishing equipment. AI-powered predictive maintenance systems can monitor vibrations, temperature, and performance to detect issues before they cause breakdowns. This reduces unplanned downtime and extends machine life.
2. Intelligent Design and Prototyping
AI can analyze customer preferences and suggest design modifications. For example, if data shows a rising demand for eco-friendly features, AI could propose layout changes that support recyclable materials or energy-saving configurations. Some AI tools even create digital twins—virtual models of products—to simulate performance before building physical prototypes.
3. Automated Quality Control
AI-driven computer vision systems scan components during and after production to detect microscopic defects, misalignments, or cosmetic issues. These systems improve quality consistency and reduce the cost of rework.
4. Supply Chain Optimization
AI can forecast demand, suggest inventory levels, and optimize sourcing strategies. It factors in weather, supplier delays, and geopolitical risks to ensure you’re never short on parts or overstocked. For instance, if a supplier of metal components is facing shipping delays, AI can suggest alternate vendors and reorder timelines to prevent production gaps.
5. Customer-Centric Manufacturing
AI enables mass customization. Customers can choose configurations via a web portal, and AI translates their selections into manufacturing instructions in real-time. This is a game-changer for manufacturers offering customized or modular products.
Limitations of Traditional Automation in Manufacturing
- Traditional automation was not designed for frequent product changes. In manufacturing, where products are often tailored to customer specifications or market trends, rigid automation systems can become a bottleneck.
- Reprogramming machines for every new variant takes time and expertise. Plus, traditional automation lacks contextual understanding. If a machine malfunctions or runs out of parts, it won’t know what to do next—it just stops.
- Also, traditional systems cannot integrate well with digital platforms. In a world that demands connected factories and real-time data sharing, this is a major shortfall.
Challenges of Implementing AI
AI isn’t a silver bullet. It involves extensive capital outlay, talents in data scientists, and quality data platforms.
- Presently, it is still evident that several manufacturing firms face the challenge of utilizing legacy systems that are not compliant with AI. These systems can therefore take a lot of time to enhance.
- There’s also a learning curve. AI must be given adequate training in order for it to get better and enhance its performance. When poorly implemented it can result into negative outcomes such as producing wrong results and creating frustrations.
- Cybersecurity is another concern. Since the AI systems mostly depend on the dependency on the internet and networks, they are prone to cyber attacks if appropriate measures are not taken.
How to Choose What’s Best for Your Business
There’s no one-size-fits-all answer. The right choice depends on your business goals, customer expectations, and product complexity.
- If your manufacturing line produces standardized goods with minimal customization and you want a quick ROI, traditional automation may be the way to go.
- However, if you aim to offer high-end, customized products and want to stay ahead of the competition with smart, flexible operations, AI is a better choice.
- In most cases, a hybrid model works best. You can use traditional automation for tasks like basic assembly or material handling and integrate AI for scheduling, quality control, and design optimization.
Real-World Example: AI in Consumer Electronics Manufacturing
Imagine that your company specializes in constructing smart appliances of various configurations based on each buyer’s needs. However, a traditional approach would have been to selectively replace the machine instructions in each variant one at a time which would slow down the process and introduce more errors.
Now, imagine using AI. Customers choose the specific things in a website, the size of the screen, the color, the internal memory, and the AI interfaces these options into electronic blueprints. Then, it directs the machines to place the component in the slots as follows:
If a part is missing or delayed, the intelligence immediately reorganizations the production process, but does not stop the line. It is only possible with AI management that step can be taken to get the agility to this level.
Workforce Considerations
Traditional automation often reduces blue-collar jobs but creates roles in machine supervision and maintenance.
- AI, meanwhile, transforms the workforce. You’ll need data engineers, AI model trainers, cybersecurity experts, and digital transformation leads.
- Retraining and upskilling your existing team is key to successfully adopting AI.
- However, AI also empowers employees. Workers can use smart dashboards to make better decisions, reduce guesswork, and improve productivity.
Future Outlook
Intelligent automation is the future of manufacturing as the concept involves the principals of both artificial intelligence and traditional automation. Smart factories are already in a process of development whereby machines, people, and systems work in unison in near-real mode. Predictions include the use of digital twins means of IoT sensors, machine learning, and computer vision as normative.
Manufacturers bring AI to bear early on for speed of innovation, personalized solutions, and business continuity.
Conclusion
Automation and AI are two different concepts, both of which have their role in solving problems and issues. Traditional systems can be classified as the best systems in the sense that they are reliable and can handle several tasks within a short span of time and at considerably cheaper prices compared to modern systems. However, as manufacturers in Brisbane and other innovation-driven cities have discovered, traditional automation is inferior when more flexibility, customization, and especially intelligent decision-making are required.
AI on the other had have the potential of enhancing your manufacturing business to provide solutions to clients; improve processes and prepare the business for future changes in the market.
In this case, the most effective approach for most businesses is not to attempt to favor one over the other but rather to adopt both. Implement traditional automation for handling recurrent and routine processes and AI for novelty, variability or the customer touch points.
The road ahead is digital, data-driven, and intelligent. Choosing the right blend of automation technologies will ensure your manufacturing business doesn’t just survive but thrives.