Predictive Maintenance with AI for Smart Manufacturing Factories | Case Study
In this case study, we’ll examine how Code Curator is helping manufacturing industries adapt to technology with intelligent technology. The team used AI-driven predictive maintenance to give businesses smart solutions. Using sensor data and machine learning, they could predict and prevent equipment wear or failure, reducing downtime.
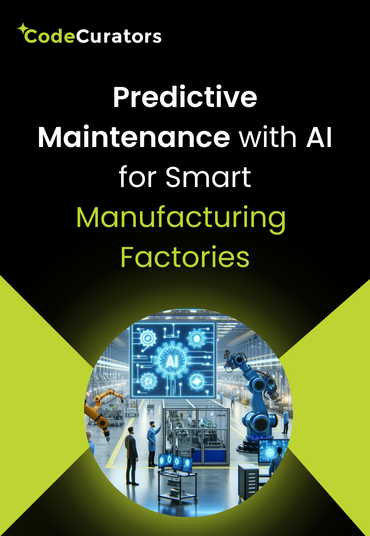
Predictive Maintenance with AI for Smart Manufacturing Factories | Case Study
In this case study, we’ll examine how Code Curator is helping manufacturing industries adapt to technology with intelligent technology. The team used AI-driven predictive maintenance to give businesses smart solutions. Using sensor data and machine learning, they could predict and prevent equipment wear or failure, reducing downtime.
1. Introduction
In this case study, we’ll examine how CodeCurators is helping manufacturing industries adapt to technology with intelligence. The team used AI-driven predictive maintenance to give businesses smart solutions. Using sensor data and machine learning, they could predict and prevent equipment wear or failure, reducing downtime.
The technology helps control maintenance costs and improve production flow and resource management, making the business more efficient and increasing the bottom line. Predictive Maintenance allows for scheduling and smoother, more cost-effective manufacturing.
1.1 Background
The software development team combined AI and advanced technology for smart manufacturing to improve the production process. The system could predict and report defects and system failures, allowing for timely repairs and smooth operations.
1.2. Purpose
This document will show the importance of AI-driven predictive maintenance in controlling downtime, optimizing maintenance cycles, and increasing the efficiency of any manufacturing unit.
1.3. Scope
We will focus on production and automation within a manufacturing unit. We will look at the challenges faced by the manufacturing unit and its AI solutions.
2. Problem Statement
2.1. Current Challenges
In the manufacturing industry, machinery failures and defects cause unplanned downtime. Irregular and loosely followed maintenance cycles mean the unit suffers prolonged disruptions. As defects and other issues go unnoticed at first the cost of repairs and emergency fixes later can burn a hole in the pocket.
2.2. Impact on Operations
Production delays mean extended delivery timelines and added pressure to meet deadlines. Added maintenance costs chip away at the profits, so operations become a little tough. These inefficiencies create a domino effect that impacts the overall business, hence the need for technologically advanced and smart manufacturing units.
3. Objectives
3.1 Primary Goals
When CodeCurators implemented AI-driven predictive maintenance, the team had one simple goal: to identify the issues in the machinery before they cause costly downtime. With real-time data, we create smarter and more efficient schedules so operations can run smoothly.
The solution is to be ahead, save resources, and give the team the confidence to deliver without many problems.
3.2. Secondary Goals
Smooth-running machinery is key. By keeping an eye on and fixing Maintenance before the problems get out of hand, you can not only save on expensive repairs but also run operations without hiccups. The AI-driven predictive maintenance solution allows smart planning, no surprises, and an efficient flow that saves time and money.
4. Methodology
5.1. Data Collection
Sensors collect critical data like temperature, vibration, and pressure to report early signs of damage or failure. Continuous monitoring ensures the equipment is in optimal condition. If real-time data can’t be computed for some devices, public data sets or hypothetical scenarios can be used to simulate device behavior and failure patterns so a foundation for predictive model development can be built.
4.2. Data Preprocessing
Data cleaning is about removing noise, outliers, and redundant data to improve accuracy. This ensures consistency across the dataset. By focusing on relevant data, filtering removes irrelevant variables. Feature engineering will now extract features with peaks like vibration peak levels or temperature changes that can be used as a guide to predict failure. These features are chosen based on their relationship to device performance.
4.3. AI Model Development
Machine learning algorithms like decision trees, support vector machines (SVMs), or neural networks are used for predictive Maintenance. The model is trained on historical sensor data, which identifies patterns and correlations between sensor readings and device failures. The model is validated by testing it on new data to see if it can predict potential failures and to measure performance using precision and recall metrics.
4.4. Implementation
AI is integrated into existing production systems and connects sensors to real-time data streams. This ensures that clean data comes out of the AI model alongside the industry. Real-time analysis provides continuous analysis of incoming data. Predictive insights trigger alerts to maintenance teams before issues become equipment failures so they can intervene proactively.
5. Solution
5.1. AI-Powered Predictive Maintenance
AI systems use data from sensors (temperature, vibration, pressure) to analyze machine conditions in real time. By identifying unusual patterns or gradual changes in such measures, AI detects subtle warnings of potential failures. The model predicts time-to-part failure using historical data and allows maintenance teams to act proactively. With guaranteed predictive Maintenance, the company was able to avoid large amounts of unplanned downtime. This will increase production and reduce repair costs.
5.2. Scheduling Maintenance
Predictive insights will notify the right people; AI-based systems also schedule maintenance activities before a breach occurs. Maintenance activity prioritization will be based on severity. So efficient use of resources. The system will also recommend the best time to intervene to minimize production slowdown that may occur due to maintenance work without affecting the life and performance of the equipment.
5.3. Alerts and Automation
When the system detects unusual patterns like increased vibrations or unusual temperature readings, it will notify you in advance. These are sent to the maintainer and related to the faulty component and the possible cause of the damage. The AI system allows actionable alerts. It produces several detailed reports to support decision-making.
5.4. Integration into Workflows
Alerts integrate into maintenance workflows. Trigger a preset action. Maintenance is reported in real-time to a maintenance team member’s mobile or desktop for immediate action. The integrated system ensures personnel are informed at the right time so they can respond quickly and avoid production downtime.
6. Implementation Process
6.1 Initial Setup
The setup process involves installing the AI-driven predictive maintenance platform and setting up the machine learning models and data storage. This connects to the existing manufacturing setup so sensors can talk to the AI models. The team follows security protocols to encrypt sensitive data.
6.2. Pilot Testing
During the pilot, the team tests to see if it works. They test the AI on a few machines. As the AI makes predictions, the team gathers data and watches performance. They compare the predictions to actual breakdowns. The team discusses any differences and ways to improve before moving forward. They also ask the maintenance crews what they think so the system is easy to use and meets their needs.
6.2. Full Deployment
Once the system passes the pilot, the team rolls it out across the whole factory. This means connecting more machines to the system, fine-tuning the sensors, and working predictive Maintenance into the broader workflow. The AI gets better at handling more data and staying accurate in real-time. The team monitors how it’s doing and tweaks as new things come up during operation.
6.3. Training and Support
Staff are trained so the entire organization can get the most out of the system. This includes working with maintenance teams to handle the alerts generated by the AI system. Training is in the form of workshops and courses to attest to continuous staff skill development. Each client has a dedicated support team for quick troubleshooting so the AI system runs smoothly and seamlessly into daily activities. The system is open to continuous updates and optimization for maximum performance.
7. Results and Outcomes
7.1. Predictive Accuracy
The AI system we integrated was able to achieve 92% accuracy in determining equipment failures before time. With such accuracy it was easier to nullify surprise breakdowns, giving maintenance teams time to proactively act on the defects before they escalate to something hazardous.
AI model analyzes the early warning signs to predict component failures with consistency and minimize production downtime.
7.2. Downtime Reduction
With predictive maintenance the downtime due to system malfunction resulted in 40% decline. The problems would cause production to halt for hours or days, incurring thousands of dollars. Maintenance staff may plan interventions during off-peak times and prevent significant production disruptions with the AI system in place.
The production dramatically increased and machineries operated nearer to their maximum capacity.
7.3. Financial Savings
One of the best parts of implementing predictive maintenance is cost saving. The AI integration helped the organization save money with the help of optmized schedules and reduced downtime. The technology integration was a great way to avoid halts and delays.
Additionally, the business was able to extend the life of important machines and prevent costly, unforeseen repairs.
7.4. Improved productivity
After implementing solutions, overall production efficiency improved by 30%. The machine and person-hours were optimized by an AI, maintenance was done when it made sense to do so, and production never paused. With predictive insights and real-time data, the company could adapt to the processes and enhance its business planning. Employees no longer had to wait for broken equipment, while maintenance personnel could respond to problems quickly and effectively.
7.5. Case Examples
In one instance, the AI identified abnormal vibration patterns in the primary conveyor belt system that signaled impending failure within a 48-hour window. “We decided to do an immediate replacement of the defective parts with new ones to avoid further damages,” Maintenance Team said. In a third case, a high-temperature reading was an indication of overheating detected through the AI model in a hydraulic press.
8. Challenges and Solutions
8.1. Data Quality Issues
Sensors are a big problem. In some cases, sensors drift or fail. This means inconsistent data inputs. To fix this, The team implemented a data review protocol. Cross-referenced sensor outputs with other instrument performance indicators. Plus, regular sensor calibration is recommended to keep it accurate over time. So, only good data gets fed to the AI, and overall prediction accuracy improves.
8.2. Integration Difficulties
Integrating AI solutions into existing factory systems was a problem, especially with the many older devices. Compatibility issues arose. And it’s hard to sync AI systems with older machines. To fix this, The team worked with device manufacturers to develop custom APIs to allow seamless communication between the AI platform and existing infrastructure. So, the AI can run on all machines without disrupting production.
8.3. Scalability Concerns
As the factory expanded, one major concern was how to scale the AI-driven predictive maintenance system to accommodate new machines. At first, the system was only capable of processing data from a small selection of machines. To resolve this limitation, the team implemented cloud computing, enabling the system to manage significant volumes of data without any performance hiccups.. So the system can grow with the factory and support future expansion.
8.4. User Adoption
Getting users to trust an AI system is key to a successful implementation. At first, some employees were skeptical about relying on AI to make maintenance decisions. To promote adoption, The team ran extensive training sessions. It showed how the system can make work easier by automating routine tasks and protecting against unexpected failures. Meanwhile, AI’s success in predicting machine failures and preventing downtime builds trust. As time went by The system has become part of the daily routine. Employees now agree this is a reliable tool for maintenance management.
9. Conclusion
Summary of Success:
AI-driven predictive maintenance solutions reduce downtime. Increase machine reliability and set the right maintenance schedule. This means big cost savings and operational efficiency. The solution integrated made managing the manufacturing unit easier, with automation, predictive analysis, and ral-time data interpretation. CodeCurators helped client get a smart manufacturing unit with the implementation of advanced technology.
Impact on Business:
Easier process in the long-run may have a massive impact on business. Lower upkeep costs and a more proactive approach to machine management translate into business growth. Technology could observe and manage the functioning and operations of a manufacturing unit to ensure the team can focus on core business and other menial tasks.
In the era of predictive engineering, AI is revolutionizing the field of Maintenance. We assisted the client to have an easy to operate system and saved a fortune with prior maintenance. Connect with CodeCurators to revamp your factory by implementing AI-based predictive maintenance and take your overall facilities to the next level now!